PRODUCTS
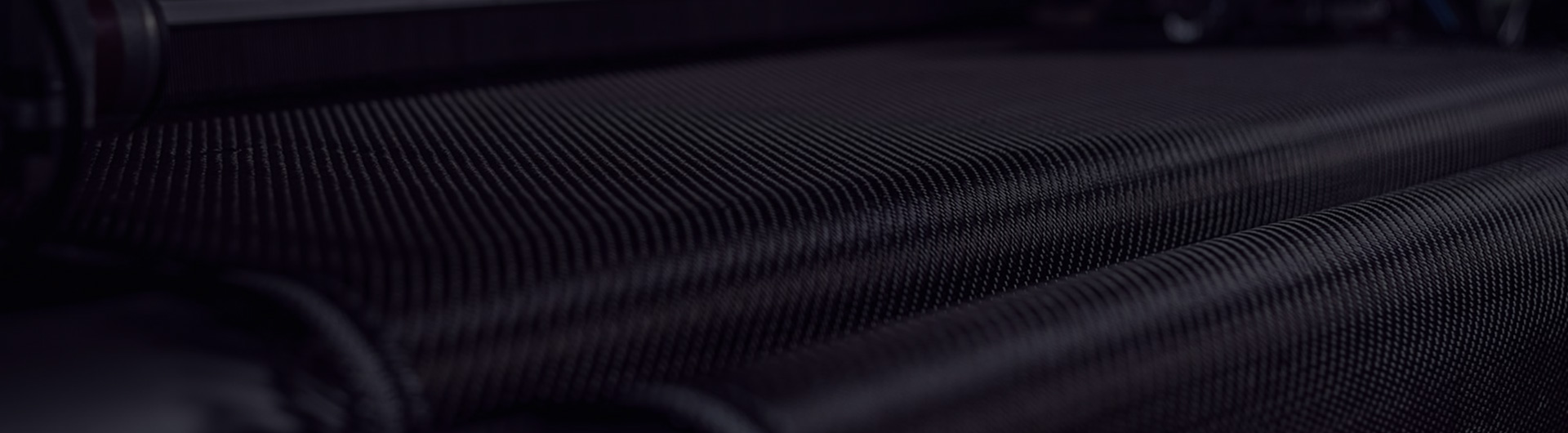
Carbon fiber bottle cage
The appearance is beautiful, stylish and generous, and the streamlined compact design can be used on any road surface. The stability of the kettle is maintained, and the kettle can be easily accessed during riding.
Production process: compression molding process. After the equipment is formed, it is polished and painted by hand.
Product parameters
Brand: FALMX
Name: Bottle cage
Material: Carbon fiber
Color: black
Outside view: 3K bright light / matte light
Applicable objects: road bikes/mountain bikes
Applicable parts: dual-purpose handlebar and frame
Product advantages
First: Super toughness, will not deform or break under strong impact,
Second: Lighter weight, lighter than metal aluminum, but stronger than steel.
Third: Carbon fiber material, which is less likely to scratch the kettle than other aluminum alloy water racks! It is perfectly streamlined and is used to carry plastic and aluminum alloy kettles. It is lightweight and suitable for all kinds of mountain bikes and road bikes.
Product details
Process description
1. Molding method
For carbon fiber is a fiber material, fiber material molding is used in the molding process of carbon fiber material. Fiber molding is a method of molding composite products by putting pre-mixed or pre-impregnated fibrous molding materials into a metal mold at a certain temperature and pressure.
2. Basic principles of forming
The rheological behavior of thermosetting plastics during the molding process is much more complicated than that of thermoplastics. The chemical reaction always accompanies the entire forming process. In the initial stage of heating, the material presents a low-molecular viscous flow state with good fluidity. As the functional groups react, part of the material is cross-linked, and the fluidity of the material gradually decreases. A certain degree of elasticity occurs and the material becomes a gel state. Then continue heating to make the molecular cross-linking reaction more perfect, the degree of cross-linking increases, and the material changes from a gel state to a glass state. Finally, the molding of the resin body structure is finished.
3. Control factors of molding
The controlling factors of molding are usually called “three elements”, namely temperature, pressure and time.
1) Temperature: This process parameter determines the heat transfer conditions from the mold to the material in the cavity, which has a decisive influence on the melting, flow and solidification process of the material.
2) Pressure: The pressure generated by closing the mold, tightening the material, promoting melt flow and balancing the volatilization of low molecular weight in the mold cavity.
3) Time: also known as compression molding heat preservation time, to ensure that the cavity shape has enough time to complete the curing.
Recommended list
Want to learn more about the company's products and information?
Enter your email address
Contact Us
Tel: +86-769-8298 7125
Fax: +86-769-8298 7126
Add.: Xiegang Town, Dongguan City, Guangdong Province, China
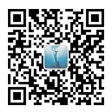
Follow Us
Copyright© 2021 Dongguan City Shangtai Carbon Fiber Technology Co., Ltd. Powered by www.300.cn
Copyright© 2021 Dongguan City Shangtai Carbon Fiber Technology Co., Ltd.